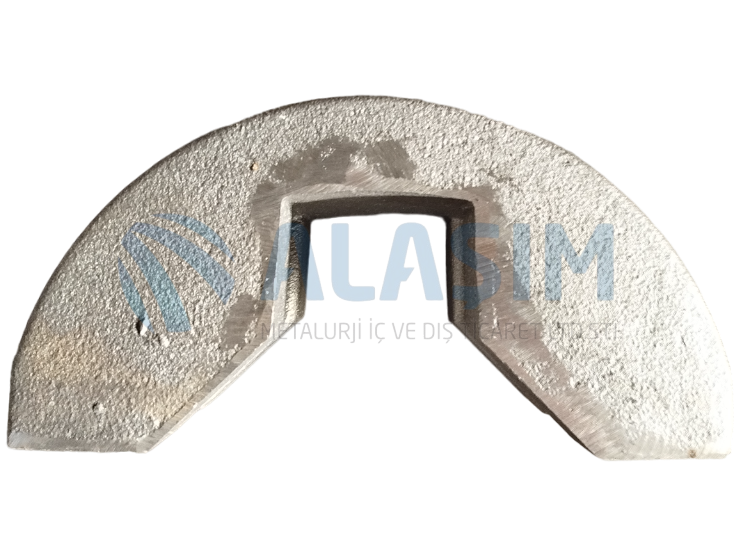
Sfero Döküm
Sfero döküm, grafit yapısının küresel (sfero) formda olduğu, yüksek mukavemet ve darbe dayanımı sunan bir dökme demir türüdür. Küresel grafit yapısı, malzemeye kırılganlığı azaltırken, esneklik ve dayanıklılık kazandırır. Kimyasal bileşiminde genellikle demir, karbon, silisyum, magnezyum ve bazen nikel gibi elementler bulunur; magnezyum, grafitin küresel yapıda oluşmasını sağlar. Bu özellikleri sayesinde sfero döküm, çelik özelliklerine yakın bir mekanik dayanım sağlarken döküm kolaylığı sunar. Sfero döküm, otomotiv parçaları, hidrolik bileşenler, borular, pompa gövdeleri gibi birçok alanda tercih edilir ve yüksek aşınma direnci, mukavemet ve işlenebilirlik avantajı sunar.
Sfero döküm, diğer adıyla küresel grafitli dökme demir, demir-karbon alaşımının özel bir türüdür ve grafit yapısının küresel (sfero) formda olduğu bir yapı sunar. Bu küresel grafit formu, sfero dökümün daha yüksek mukavemet, esneklik ve darbe dayanımı göstermesini sağlar. Sfero döküm, demir döküm ürünlerinde kırılganlığı azaltarak çeliğe yakın mekanik özellikler sunan bir malzeme olarak bilinir. Özellikle dayanıklılık ve kırılmaya karşı direnç gerektiren uygulamalarda tercih edilen bu döküm türü, üretim süreçlerinde de geniş bir kullanım alanına sahiptir.
Kimyasal Bileşim ve Yapı
Sfero dökümün kimyasal bileşiminde genellikle demir, karbon, silisyum, mangan ve magnezyum bulunur. Magnezyum, döküm sırasında karbon atomlarının küresel yapıda birleşmesini sağlayarak grafitin küre formunda kalmasını sağlar. Bu küresel grafitler, malzemenin esnekliğini artırır ve mekanik yük altında çatlama olasılığını azaltır. Bu sayede, sfero döküm, geleneksel dökme demirlerden daha yüksek bir mukavemet sunar ve kırılganlığa karşı dayanıklıdır. Ayrıca, kullanılan diğer alaşım elementleri, malzemenin dayanıklılığına, aşınma direncine ve işlenebilirliğine katkıda bulunur.
Fiziksel Özellikler
Sfero döküm, diğer dökme demirlere göre yüksek dayanıklılık, esneklik ve darbe direnci sunar. Bu özellikleri sayesinde ağır yük taşıyan parçalarda ve yüksek mukavemet gerektiren uygulamalarda sıklıkla tercih edilir. Ayrıca, sfero dökümün mekanik özellikleri, çelikle kıyaslanabilir seviyededir; ancak çelikten daha düşük maliyetle döküm yapılabilmesi, onu daha ekonomik bir alternatif yapar. Düşük sıcaklıklarda bile çatlama riski azdır ve malzeme, geniş bir sıcaklık aralığında güvenle kullanılabilir. Yüksek aşınma direnci ve sertlik, sfero dökümü uzun ömürlü ve dayanıklı bir malzeme yapar.
Isıl İşlem ve Performans
Sfero döküm, çeşitli ısıl işlem süreçlerinden geçerek performans özellikleri artırılabilir. Tavlama, sertleştirme ve normalleştirme işlemleri, sfero dökümün mukavemetini, sertliğini ve dayanıklılığını optimize etmek için yaygın olarak uygulanır. Bu ısıl işlemler, malzemenin iç yapısındaki karbon ve ferrit-perlit oranlarını ayarlayarak, dökümün kullanım amacına göre özel özellikler kazandırır. Isıl işlemle, darbe dayanımı ve aşınma direnci artırılabilir, böylece malzemenin özellikle zorlu endüstriyel uygulamalarda uzun ömürlü performans sergilemesi sağlanır.
Kullanım Alanları
Sfero döküm, otomotiv, inşaat, hidrolik ve petrol endüstrisi gibi pek çok alanda yaygın olarak kullanılır. Özellikle krank milleri, kam milleri, dişli kutuları, borular, hidrolik bileşenler, pompa gövdeleri gibi yüksek dayanıklılık ve esneklik gerektiren parçalarda tercih edilir. Otomotiv sanayisinde sfero döküm, çelikle kıyaslanabilir özellikler sunarken daha uygun maliyetli bir seçenek olarak öne çıkar. Ayrıca, sfero döküm, düşük sıcaklıklarda bile çatlama riski taşımaması sayesinde, yüksek mukavemet ve dayanıklılık gereken boru sistemleri ve taşıma ekipmanlarında güvenle kullanılır.
Avantajlar ve Zorluklar
Sfero dökümün en önemli avantajları, yüksek mukavemet, esneklik ve ekonomik üretim sürecidir. Çeliğe yakın dayanıklılık sunarken daha düşük maliyetle üretilmesi, sfero dökümü çok yönlü bir malzeme haline getirir. Ayrıca, şekillendirilebilirliği, bu malzemenin karmaşık geometrik şekillerde dökülmesini kolaylaştırır. Ancak, yüksek nitelikli ısıl işlem ve döküm teknikleri gerektiren üretim süreci, belirli bir uzmanlık ve dikkat ister. Magnezyumun kontrollü miktarda eklenmesi ve doğru ısıl işlemlerin uygulanması, malzemenin istenen kaliteyi sağlaması için kritik öneme sahiptir.