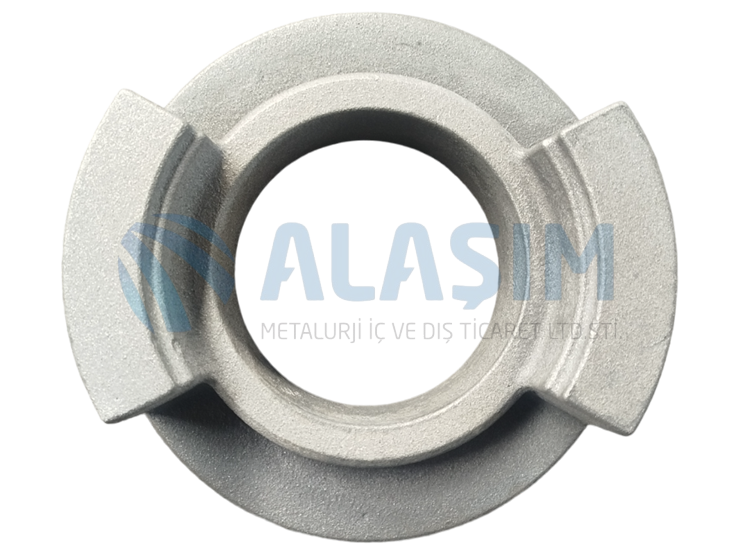
Nodular cast iron
Nodular cast iron is a type of cast iron that has a spherical (spheroidal) graphite structure and offers high strength and impact resistance. The spherical graphite structure reduces the brittleness of the material while providing flexibility and durability. Its chemical composition usually includes elements such as iron, carbon, silicon, magnesium and sometimes nickel; magnesium ensures that the graphite forms in a spherical structure. Thanks to these features, nodular cast iron provides a mechanical strength close to steel properties while offering ease of casting. Nodular cast iron is preferred in many areas such as automotive parts, hydraulic components, pipes, pump bodies and offers the advantage of high wear resistance, strength and workability.
Ductile iron, also known as spheroidal graphite cast iron, is a special type of iron-carbon alloy and offers a structure in which the graphite structure is in a spheroidal (spheroidal) form. This spheroidal graphite form allows spheroidal iron to exhibit higher strength, flexibility and impact resistance. Ductile iron is known as a material that offers mechanical properties close to steel by reducing brittleness in iron casting products. This type of casting, which is especially preferred in applications requiring durability and resistance to breakage, also has a wide range of uses in production processes.
Chemical Composition and Structure
The chemical composition of ductile iron generally includes iron, carbon, silicon, manganese and magnesium. Magnesium allows the carbon atoms to combine into a spherical structure during casting, allowing the graphite to remain in a spherical form. These spherical graphites increase the flexibility of the material and reduce the possibility of cracking under mechanical load. In this way, ductile iron offers higher strength than traditional cast irons and is resistant to brittleness. In addition, other alloying elements used contribute to the material's durability, wear resistance and workability.
Physical Properties
Ductile iron offers high durability, flexibility and impact resistance compared to other cast irons. Thanks to these properties, it is often preferred in heavy-duty parts and applications requiring high strength. In addition, the mechanical properties of ductile iron are comparable to steel; however, the fact that it can be cast at a lower cost than steel makes it a more economical alternative. The risk of cracking is low even at low temperatures and the material can be used safely in a wide temperature range. High wear resistance and hardness make ductile iron a long-lasting and durable material.
Heat Treatment and Performance
Ductile iron can be subjected to various heat treatment processes to increase its performance properties. Annealing, hardening and normalizing processes are commonly applied to optimize the strength, hardness and durability of ductile iron. These heat treatments adjust the carbon and ferrite-pearlite ratios in the internal structure of the material, giving the casting special properties according to its intended use. Impact resistance and wear resistance can be increased with heat treatment, thus ensuring that the material exhibits long-lasting performance, especially in demanding industrial applications.
Areas of Use
Ductile iron is widely used in many areas such as automotive, construction, hydraulic and petroleum industries. It is especially preferred in parts that require high durability and flexibility such as crankshafts, camshafts, gear boxes, pipes, hydraulic components, pump bodies. In the automotive industry, ductile iron offers properties comparable to steel while standing out as a more cost-effective option. In addition, ductile iron is safely used in piping systems and transportation equipment that require high strength and durability, as it does not carry the risk of cracking even at low temperatures.
Advantages and Challenges
The most important advantages of ductile iron are its high strength, flexibility and economical production process. Offering durability close to steel while being produced at lower cost, ductile iron is a versatile material. In addition, its formability makes it easy to cast this material in complex geometric shapes. However, the production process, which requires high-quality heat treatment and casting techniques, requires a certain level of expertise and attention. Adding magnesium in controlled amounts and applying the correct heat treatments are critical for the material to achieve the desired quality.