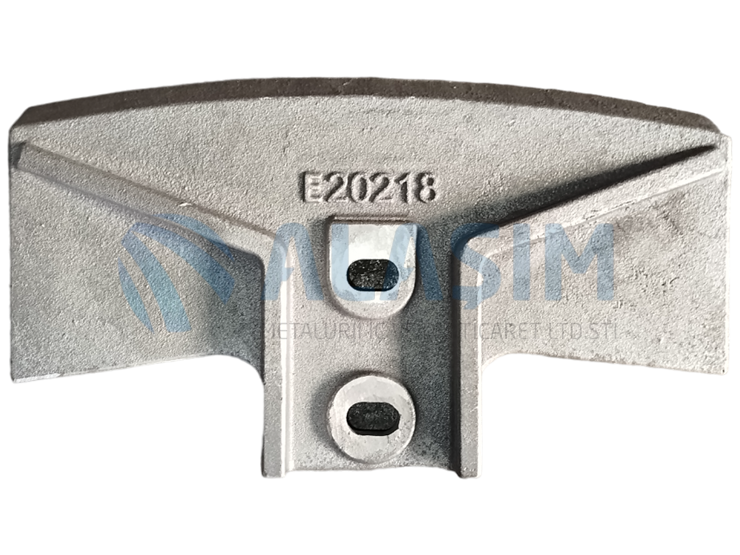
Ni-Hard cast irons
Ni-Hard cast irons are a type of alloy that provides high strength and long-lasting performance, especially in corrosive environments. This material has a composition of iron, carbon and nickel and usually contains 4-6% nickel. Nickel is an important element that determines the properties of this alloy, because it provides the material with both mechanical strength and resistance to high temperatures. Ni-Hard cast irons are generally used in the production of wear-resistant parts, and these properties make them indispensable, especially in industrial applications.
Ni-Hard cast irons are an alloy produced for the purpose of providing high durability and long-lasting performance, especially in corrosive environments. Thanks to their high nickel content (usually 4-6%), these cast irons offer excellent wear resistance and high temperature resistance. Their chemical composition includes iron, carbon and nickel, as well as low amounts of manganese, silicon and phosphorus, which increases the durability of the material. The microstructure of Ni-Hard cast irons contains martensite, pearlite and carbide phases, which give them high hardness, impact resistance and machinability. These features make Ni-Hard cast irons indispensable in demanding industrial applications such as stone crushing machines, cement factories and mining processing equipment.
Chemical Composition and Structure
The chemical composition of Ni-Hard cast irons may also contain low amounts of manganese, silicon and phosphorus, in addition to iron, carbon and nickel. While nickel increases the mechanical properties and high temperature resistance of the material, it also provides the material with a more homogeneous microstructure thanks to its nickel content. The microstructure of Ni-Hard cast irons generally contains a combination of martensite, pearlite and carbide phases. This structure provides the material with high hardness, wear resistance and impact toughness.
Physical Properties
Ni-Hard cast irons are known for their high hardness and wear resistance. These properties make them particularly suitable for use in heavy industrial machinery such as stone crushers, cement plants, and mining processing machines. In addition, Ni-Hard cast irons offer high performance even under harsh operating conditions by offering high temperature resistance and resistance to oxidation. The addition of nickel gives the material better workability and a lower tendency to brittleness, which makes them advantageous in certain production processes.
Heat Treatment and Performance
Ni-Hard cast irons can undergo heat treatment processes to provide high hardness and strength. Hardening and tempering processes increase the mechanical properties of this material, optimizing the surface hardness and internal structure. Heat treatment also increases the impact resistance of the material, making it more resistant, especially to abrasive surfaces. The machinability of Ni-Hard cast irons can be further improved by heat treatment, making it possible to use them in more complex shapes.
Areas of Use
Ni-Hard cast irons are widely used for machines operating in corrosive environments and carrying high mechanical loads. This alloy stands out in applications such as stone crushers, mining equipment, cement production plants, mills and conveying systems. The high wear resistance and durability of Ni-Hard cast irons make them the preferred materials for such heavy industrial machines, especially for long-term operations. It can also be used in less corrosive environments such as agricultural machinery, mill blades and truck equipment.
Advantages and Challenges
The most obvious advantage of Ni-Hard cast irons is their excellent resistance to wear and high temperature resistance. In addition, this material provides high hardness and durability with appropriate heat treatment, offering long-lasting and efficient use. However, Ni-Hard cast irons can be more difficult to process and shape due to their high hardness, so careful planning and expertise are required in the production process. When the durability of the material is combined with the right design and production techniques, highly efficient and economical results can be achieved.