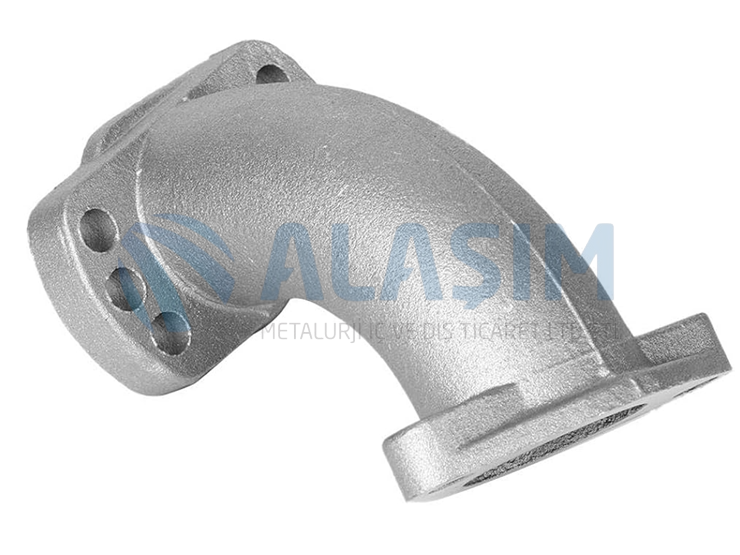
Cast Steel
Cast steel is a type of casting material that offers high strength, durability and flexibility. In addition to iron and carbon, it contains alloying elements such as manganese, silicon, chromium, and nickel; these elements increase the corrosion resistance, hardness and wear resistance of the material. Cast steel stands out with its higher impact resistance compared to other casting types and its lack of risk of cracking even at low temperatures. Steel casting, whose hardness, durability and toughness properties can be optimized with heat treatment, is used in many applications such as gears, pump bodies, valves, shafts and structural parts in the automotive, construction, mining, energy and machinery industries.
Cast steel is a casting material formed by combining iron and carbon in certain proportions and increased in strength by adding various alloying elements. Cast steel is known as a preferred material especially in applications requiring high strength, impact resistance and flexibility. The carbon ratio is usually between 0.1-0.5% and is strengthened with alloying elements such as manganese, chromium, nickel and molybdenum. These features make cast steel a common option in industrial and structural applications.
Chemical Composition and Microstructure
Steel castings contain alloying elements such as manganese, silicon, chromium, nickel and molybdenum, as well as carbon. These elements improve various properties of the material: Manganese increases strength, while chromium and nickel provide corrosion and wear resistance. Molybdenum helps cast steel maintain its shape even at high temperatures. Phases such as ferrite, pearlite or martensite may be present in its microstructure; these phases contribute to the strength and hardness of the material, depending on the alloying elements used and the applied heat treatments. Steel castings are a material whose structural properties can be optimized with appropriate heat treatments.
Physical and Mechanical Properties
Steel casting stands out with its high strength, impact resistance and flexibility. Thanks to these features, steel casting can be used safely in load-bearing parts and in corrosive environments. It has high resistance to impacts even at low temperatures and does not carry the risk of breakage. The high wear resistance of steel ensures that steel casting parts are long-lasting and durable. At the same time, hardness and toughness can be increased by applying heat treatment, which makes steel casting suitable for heavy industry applications.
Heat Treatment and Performance Improvement
Steel casting is a material whose properties can be improved by various heat treatments such as annealing, hardening, and normalizing. These processes optimize the microstructure of the steel casting and increase properties such as strength, hardness, and wear resistance. In particular, tempering and quenching processes are used to increase the impact resistance and hardness of the steel casting. After heat treatment, the steel casting becomes more resistant to complex mechanical stresses and provides long-lasting use.
Areas of Use
Steel casting is widely used in the automotive, construction, mining, energy and machinery industries. It is especially suitable for parts requiring high strength such as engine parts, gear boxes, pump bodies, valves, shafts, and carrier structural elements. The impact resistance and wear resistance of steel casting allow it to be used in harsh conditions. In addition, steel casting is preferred in power plants and heating systems because it can maintain its strength even at high temperatures.
Advantages and Disadvantages
The most important advantages of steel casting include high durability, corrosion and wear resistance, and performance over a wide temperature range. However, its formability and cost advantages in the casting process also make it attractive for industrial applications. However, the production of steel casting requires expertise and a meticulous control process, as it requires precision casting processes and heat treatment processes. If steel casting is not processed correctly, cracks may occur in its microstructure or the material may not reach the expected strength level; therefore, quality control processes are of great importance.