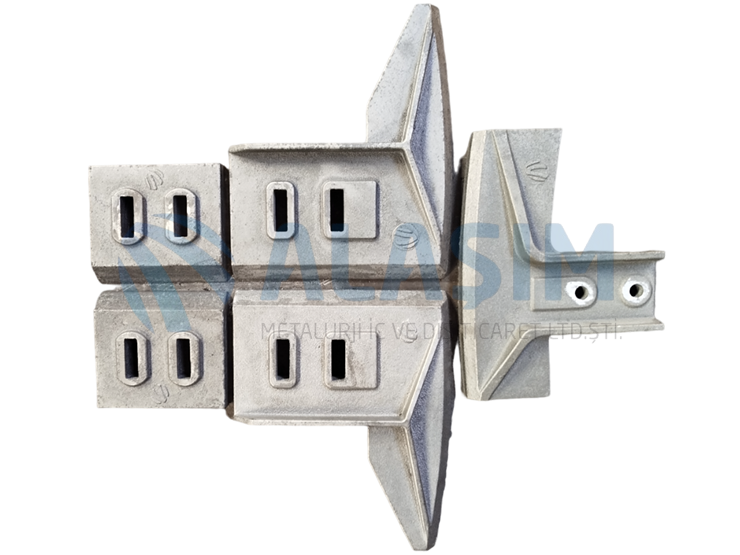
High chromium white cast irons
High chromium white cast irons are special alloys generally known for their high wear resistance and superior mechanical properties. This material is obtained by adding chromium to the alloy of white cast irons, another type in the cast iron class. The high chromium content significantly improves the properties of this material and makes it ideal for parts used in corrosive environments and harsh operating conditions.
High chromium white cast irons are resistant to high temperatures and extremely resistant to wear thanks to the carbon and chromium they contain. These materials have chemical components that must be controlled very carefully during casting. Compared to steel, this alloy has better wear resistance and is ideal for long-term use under harsh conditions. In addition, the martensitic microstructure in the structure of this alloy increases resistance to impacts.Chemical Properties and Composition
The chemical composition of high chromium white cast irons contains a high content of chromium (usually between 12% and 30%), which gives the material excellent wear resistance. In addition, the carbon content is usually high, which increases the hardness of the material. In addition, elements such as manganese, silicon and phosphorus are present in small amounts and affect the mechanical properties and machinability of the material. Chromium also increases the high temperature resistance of this alloy and improves its oxidation resistance.
Physical Properties
High-chromium white cast irons are quite hard and brittle due to their high carbon content. This makes them durable in corrosive conditions, but also makes them difficult to shape and machine. However, the presence of chromium further increases this hardness, and the material is used to produce long-lasting parts in rock crushing, mining machinery, cement plants and other heavy industry applications. The microstructure of white cast irons usually contains a combination of martensite and carbide phases, which increases wear resistance.
Heat Treatment and Performance
High-chromium white cast irons can be further strengthened by heat treatment. Hardening and tempering processes, in particular, are widely used to optimize the mechanical properties of these materials. These processes increase surface hardness, making the material more resistant to impact and friction. Heat treatment also increases the homogeneity of the material's internal structure, allowing it to perform more consistently and reliably.
Areas of Use
High chromium white cast irons are generally used in corrosive environments and applications carrying high mechanical loads. This alloy is especially preferred in stone crushing machines, mining equipment, cement factories, metalworking machines and machines operating at high temperatures. It is also widely used in areas where cast iron parts are less worn and have a longer life. Chromium is also resistant to the effects of hot and corrosive environments thanks to the material's resistance to oxidation.
Advantages and Challenges
The biggest advantage of high chromium white cast irons is that they offer excellent resistance to wear, making them cost-effective and long-lasting. However, due to their hard and brittle structure, this material can be difficult to machine and shape. Therefore, it is necessary to apply the correct heat treatment techniques during production and to make careful choices during the design phase. In addition, due to the high chromium content, the casting process of this alloy must be meticulously controlled.